工控平台上位机可根据陀螺仪获取的当前工作面数据与目标刀数据进行三
维建模,从而形成“三维数据模型”,在割煤过程中,marco 可通过读取煤机实
时数据和陀螺仪反馈的煤机实时数据进行割煤。所有卧底量、提刀量、采高可通
过 marcoifc 平台算法结合规划路径实现;在煤机司机跟机过程中,可根据实际割
煤情况,通过支架控制器适当调整下一刀或后几刀的局部数据,从而生成新的三
维模型。并且三维模型具有纠错功能,以保证工作面平稳推进。
随着程序及工艺的进一步测试优化,从开始 3 小时 40 分钟割 2 刀煤,到稳
定在 3 刀 3.5 小时完成,单班最大割煤刀数 7 刀。该智能化综采工作面实现了全工作面程序割煤和跟机自动化,普通综采工作面人工操作时,工作面正常作业人
员至少需要 11 人,采用智能化回采后,工作面单班生产仅需要 5 人,煤机、支
架巡视工 1 人、班长 1 人、机头、机尾巡检各 1 人、控制台需要 1 人,工作面人
员主要是调整和监护设备运行,设备所有动作自动完成。项目的顺利实施,促进
了煤矿开采技术的进步,探索了一条工作面智能化开采的路子,对探索中厚层工
作面智能化开采的推广具有重大意义,同时也为解决蒙陕地区煤层具有冲击倾向
性矿井地安全高效开采问题提供了新思路。
附件:纳林河二号煤矿基于地质融合惯导的智能综采系统-中煤西北能源化工集团有限公司
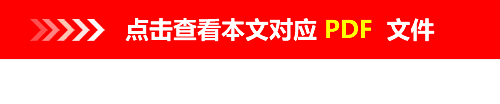
顶煤破碎及运移全历程模拟技术;采放协调智能放煤工艺及方法方面;智能化放煤控制关键技术与装备方面,实现了厚煤层综放工作面放煤机构精准监测
通过优化液压支架自动跟机 61 个关键参数,调整抬底和降抬底延迟时间等方法,实现支架动作的快准稳,单架 移架时间全部控制在 9s 以内
实现了利用“CT”切片技术生成规划切割曲线功能,切割曲线包括有等间 距网格点的煤厚,顶底板倾角,俯仰角等信息,自动生成之后 10 刀的规划曲线
顺槽带式输送机采用全硫化工艺+重型热浸镀锌支架 +高分子托辊,提高带面服务寿命,每天可减少维护人员 2 人,利用 AI 智能摄像仪配合线型激光标定光源方式,实现智能调速
劳动组织由放顶煤开采时三八制调整为四六制,日工效达到 145.8 吨/人,工作面回采率由放顶煤时 93%提升至 97%,增加 4%
开展三维地震数据和钻孔数据的质量控制分析工作;利用钻孔与地震标定建立三维地震数据与钻孔数据的联系;对开采区内煤系地层进行精细地质建模
采用先进的 LASC 高精度三维惯导系统对采煤机进行定位;开发适用于综放工作面高粉尘环境的采集频率大于 20 帧/s,COMS 传感器靶面尺寸 2/3 英寸的智能摄像头
在自动防卡钻电液控制系统中,PID 控制器用于回转压力的控制。控制器设 定值为 16MPa,输入值为油压传感器实时反馈的回转压力值
果创新了全断面敞开式掘进机智能掘进工艺技术体系,实现了 复杂地质条件下全断面敞开式掘进机施工超长(>5000 m)斜井施工
盾构机通过在 81405 高抽巷的成功应用,单日最高进尺完 成 51m,刷新了全国同类巷道最高生产纪录,月最高进尺完成 641m,平均班进 10.13m,最高班进 28.2m
改变了矿井掘进的生产模式,真正让掘进智能化与矿井 信息化无缝连接,显著提高了矿井掘进工作面设备的自动化程度
快速掘进技术的应用将传统成巷周期由 10 个月缩短到 4 个月,采煤工作面巷道形成周期缩短了 60%,大幅度降低了掘巷周期和巷 道维护费用
利用惯性导航技术实现连采机定位、定姿,利用激光导引技术与惯性导航 互为基准,连续测量,实现卷缆车自动收放缆线距离
建立了截割机器人与护盾式临时支护机器人之间的稳定性模型,研发了集 成于护盾式临时支护机器人中的全宽横轴截割机器人
开发智能化掘进工作面视频画面拼接系统,投入使用高清宽光谱、红外摄像 仪,高粉尘复杂现场环境下,可清晰展示掘进机机身和周边环境
通过以太网采集掘进工作面连运的跨转信号,精确掌握工作面出煤时间,利用霍尔传感器采集胶带机的运行电流,精准判断胶带机带面上的煤量多少